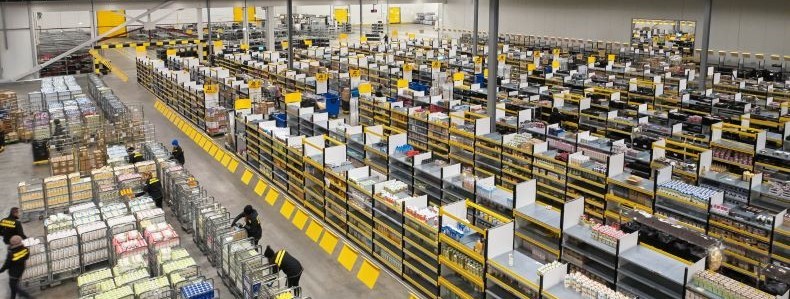
Jumbo Supermarkets Case Study
14/11/2023
Background
With almost 700 stores and approximately 100,000 employees, Jumbo has experienced significant growth during the past few years after acquiring several leading Dutch brands, including La Place, C1000 and Emté. It has more than tripled its market share over the last decade, dominating just over one-fifth of the overall market and increasing turnover by nearly 400%. Its strong foothold as the number one omnichannel food player in the Netherlands, combined with its innovative approach and core values, was established by offering the best quality and the best service, at the lowest price.
Business need
To address changing market conditions and keep pace with customer demand, Jumbo ventured into on-line shopping in 2014. This transition, in conjunction with its stores and those of its franchisors, served as a catalyst for rapid growth. Apart from traditional distribution centers and a new fully automated one, Jumbo also invested in E-fulfilment Centres (EFCs), as well as eight hubs that are operational in large towns and cities to manage the rise in demand. There are currently two EFCs where all the order picking for eCommerce takes place, with pick-up and home delivery points for groceries. The third was opened in January 2021 because of continued demand. These EFCs are located throughout the Netherlands and are very large (approximately 40,000 m²), to accommodate an extensive variety of goods that would not be available in every store. To collect customer orders as quickly as possible, Jumbo has implemented automation and constantly looks for quality and productivity improvements. Scanning technologies are used to efficiently process orders. By implementing the new technology, they have become more future proofed and this will enable to support further growth with increased up-times.
Solution
Jumbo clearly recognized the need for a innovative solution that would sustain their expansion plans and found the right one in the Honeywell CT40 wearable solution. Furthermore, Lexter provided integration of the bluetooth button to trigger the CT40 scanner within this project. Jumbo had previously worked with Honeywell as the provider for several of their in-store, distribution centre, pick-up point and home-delivery vans data collection solutions. In fact, the relationship extends far beyond a retailer and supplier one, with Jumbo including Honeywell in its IT roadmap and viewing Honeywell as an expert technology partner. After a period of six months of testing, Honeywell was selected as the preferred solution supplier.
The Honeywell solution provided higher productivity results and was deemed easier to use since it was a touch screen with a larger screen size. It didn’t require a separate ring scanner and could scan straight from the wrist with the omni-directional scanner, thus being ergonomic. Furthermore, built on the Mobility Edge platform, the futureproof solution which is upgradeable through Android, provided a lower total cost of ownership due to the longer lifecycle, thereby maximizing return on investment. Using the Mobility Edge platform, the customer can easily deploy the devices within their facility. Jumbo already had several other form factors based on Mobility Edge, so standardising on this platform proved to be key since all devices could be managed in the same way, thereby providing more cost savings. In addition, Jumbo has incorporated Honeywell CT60 mobile devices and VM1A forklift mobile computers in to their distribution centers. They have deployed the Honeywell CN80 mobile devices across their new fully automated distribution center in Nieuwegein. Jumbo is using ultra rugged CK65 mobile devices in their cold chain storage operations and CT60 mobile devices in all their stores for shop-floor mobility applications. They have also deployed Honeywell mobile and tracking devices in their vehicles across their supply chain network.
The project was deployed in less than 3 months by Honeywell, in close collaboration with its partner Simac Retail, a company located in the Netherlands providing high-quality IT services and technology for improving the business processes of large and medium-sized organisations.
Results
Overall, with the new solution deployed, Jumbo has been able to benefit with approximately 15% productivity improvements. Their employee satisfaction levels have increased due to the ergonomic design of the provided solution. Furthermore, Jumbo has noted an 8% improvement in the number of units in repair since the new solution has been deployed. With the opening of the third EFC in 2021, and the eCommerce market continuing to thrive, Jumbo is well on its way to achieving its goals.